by Pamela Paci (From Superyacht Digest | October Issue 2019 / LINK)
Last July we had the opportinuty to explore the captivating world of the 3d scale models. We visited the Italian company Model Maker Group, based in Itri, near Rome, a reference for the luxury yachting sector for years. Throughout this interview you will discover the principles and philosophy driving the company, which stands out for quality, research, cutting-edge techniques as well as a fair amount of genius whose lack would make impossible to do business right.
In the issue of April 2019 (entitled Wonderland / LINK) we had already dedicated a wide article to this firm of central Italy, where we found the typical values of the Italian craftsmanship, such as passion and commitment, as well as creativity, spirit of innovation and international scope. Our visit was dictated by the wish to know closely all the areas of the company, from the study of projects to the manufacturing process, without omitting the organizational and logistic aspects of the headquarters but above all people and interaction between the various operating areas and management.
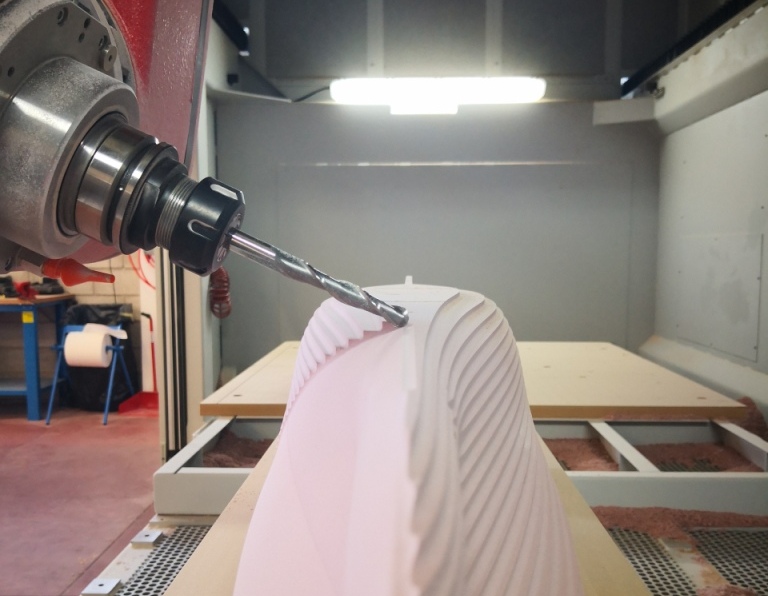
Once arrived in Rome, the city of Itri can be easily reached by any means: Model Maker Group is structured on two different facilities, not far from one another. In the new headquarters, Model Maker Group has focused part of the activities related to the processing with milling machine, while in its historical headquarters all the various steps of the manufacturing process until the dispatch to customers are performed. Here there are also the administrative offices.
Model Maker Group is today an internationally renowned business: with an experience gained in 16 years of activity, the company moved its first steps in a small garage to reach nowadays an international consolidated position.
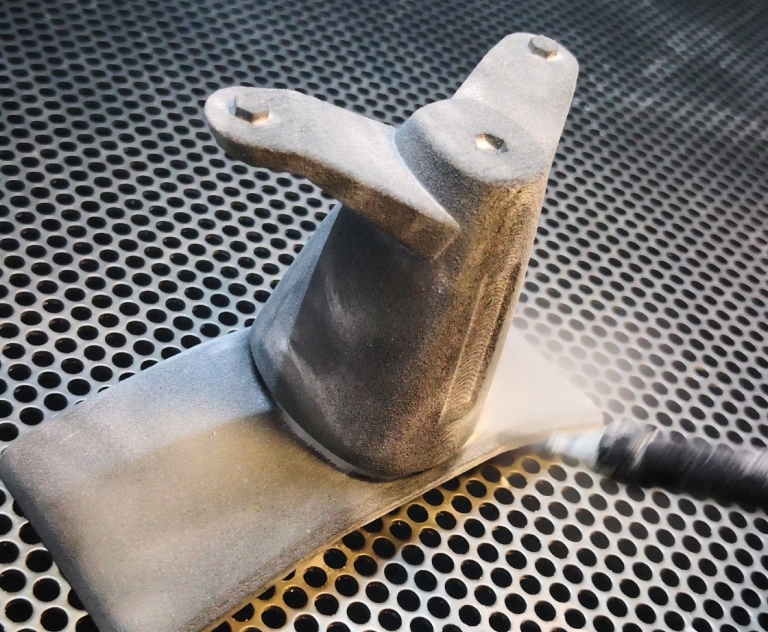
Over these years, the management has been able to develop an excellent organization, with a team of 21 people including partners and specialised model makers, able to ensure the best quality of the product currently on the market.
During our visit we talked to managers and employees to collect the following interview in which they explain what is behind fine scale model yachts and how they are built.
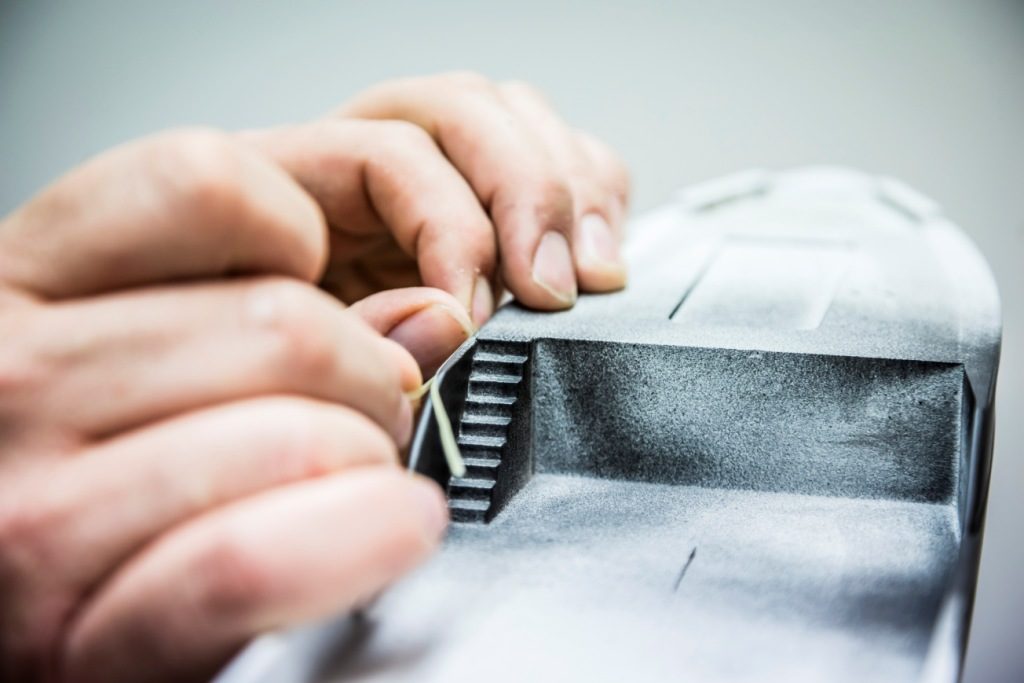
Interview with Elisabetta Fantasia (CEO)
We found it pleasant to realise that your headquarters, halfway between Rome and Naples, can be easily reached by any means, an important aspect. Does it often occur that customers come to visit you?
EF: “Yes, it often occurs that customers come to visit us to follow the implementation of their miniature project. Over the recent years, the number of visits at our company has remarkably increased: this is the perfect occasion for us to show proudly the reality we have built. We are always delighted to note how everyone is pleasantly surprised by seeing with their own eyes how structured and complex can be a company realising scale prototypes. A real SME and not a simple craft workshop”.
How is the company structured from an organizational perspective and how do you manage your relationship with a customer at the beginning stage and during the process?
EF: “At the beginning stage, the first contact is managed by Giuseppe Capobianco who, as Sales & Operation Manager, is the reference point for the entire process. Later, the Account takes care of any organizational and bureaucratic aspects, while Mario Moses, our Project Development Specialist, becomes the interlocutor for technical details of the realisation, acting as go-between for customers and coordinators of our production departments”.
How are the manufacturing operations split and what are the most delicate aspects of each and every operation?
EF: “Our manufacturing process is broken down into specific areas, each one with its specialisation. Our model makers are divided according to their tasks: engineering office, milling department, sanding department, painting department, finishing and assembly department, plus the logistic, administration and marketing offices. Each department has its own peculiarities, from perfection of sanding in the tiniest components to the mastery to reproduce, among thousands of shades, the exact colour chosen by the customer. But everyone has a common characteristic: here the model makers’ accuracy and concentration are essential”.
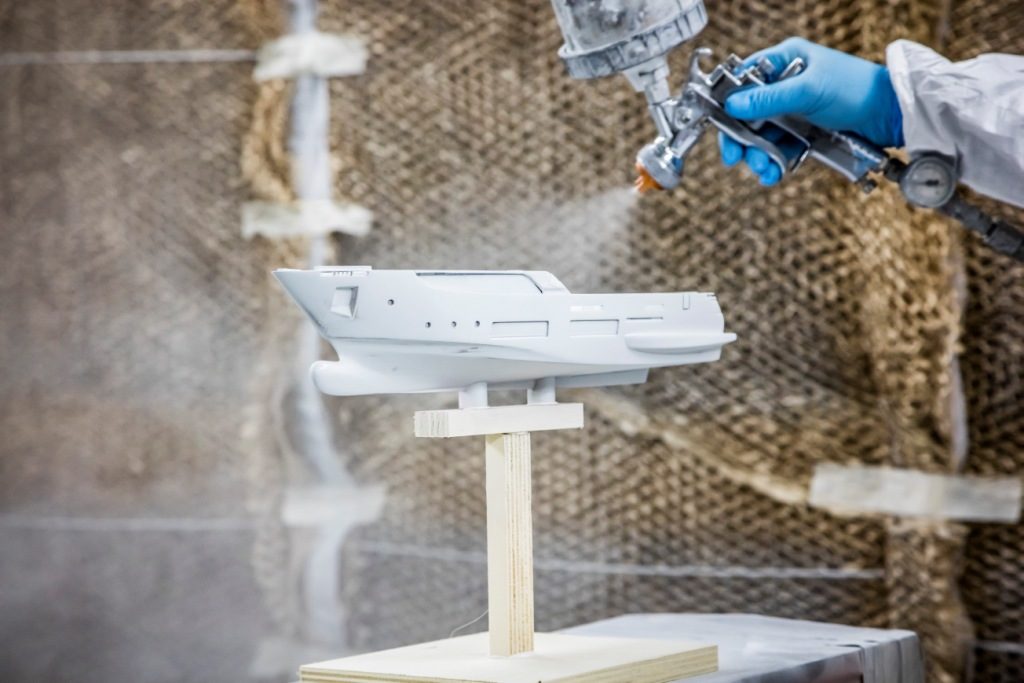
Interview with Giuseppe Capobianco (Sales & Operation Manager)
How could you turn a small handicraft business into a so well-structured company with cutting-edge techniques and above all so well positioned in the market to have a leading role?
GC: “We have never lacked ambition. By joining a quality job with the know-how of a qualified team, plus an entrepreneurial perspective of ongoing growth and improvement, part of the success is already set out. We have always given a lot of importance to customers and our availability for them: we are present at the most important yachting trade shows to ensure an assistance going beyond the realisation and delivery of the model. To answer and meet always the requirements of those who choose us. Our last important investment in the purchase of a new five-axis milling machine is the confirmation. We constantly renew ourselves to face in an increasingly efficient way the market requests and keep high the value of our brand. We want to be known not only for our ten-year experience in this sector but also and above all because the quality of our products meets high standards and keeps improving over the years”.
How are your productions differentiated? We have seen creations of mass-produced models but also custom realisations and even as built products?
GC: “Our yacht models are usually divided into categories: mass-produced products, or rather standard models of projects, marketing models, custom models realised for shipyards for this purpose (thus for exhibitions in trade shows, for events, etc.) or study models, concept models realised to assess mainly shapes, volumes and paint-schemes of projects. Besides these categories there are also the so-called as-built realisations: faithful reproductions of megayachts already launched”.
When you interface with a customer, either a shipyard or an architect, how do you know that you are doing an excellent work, how do you measure their level of satisfaction?
GC: “As Elisabetta confirmed before, we often host customers for a meeting on work progress. When this does not occur, we keep anyway a direct contact with our customers by keeping them frequently updated about the work we are realising for them. A so developed customer care is essential to meet in the best possible way the customers’ needs and realise exactly the prototype imagined by them. When the model is delivered, we always make sure in person that they are satisfied and often the customers send us their voluntary feedback for our work”.
How have the manufacturing methods changed from when you started to this day and what innovations will the future bring?
GC: “The manufacturing methods have changed a lot: we started from our hands, without big technologies for the realisation of our prototypes and this allowed us to be able to make the most of the machines. Starting from a handicraft condition in all respects, we have learned to identify problems and use our ingenuity to solve them: from manual dexterity to technology we have developed skills that we would have never had if we had followed the opposite path. This is a luck for us. Over the years, the new technologies have joined the tools that we used at the beginning, sometimes even replacing them: but having experience of the origin gives us an extra skill that allows us to find always a solution to a complex situation. Of course, the future will bring new ones, and we are ready to make the most of them”.
As regards the materials, we have seen that you use first-quality resins. How can you make research in this area?
GC: “We visit lots of trade shows and we keep ourselves updated about the latest news, because there is no manufacturing standards to be followed. The manufacturing process used by us is defined by us, the outcome of years of experience, experiments and new solutions. The choice of materials is essential for a successful work and it is important also to be able to identify which material is the best for the realisation of each and every part, from the main deck to the sundeck as well as all the furniture and decorations such as miniature plants, paintings and accessories. The materials used today are those with the best performance that we have found over these years, but in the future, we do not exclude that they could be others. The technology is in constant evolution”.
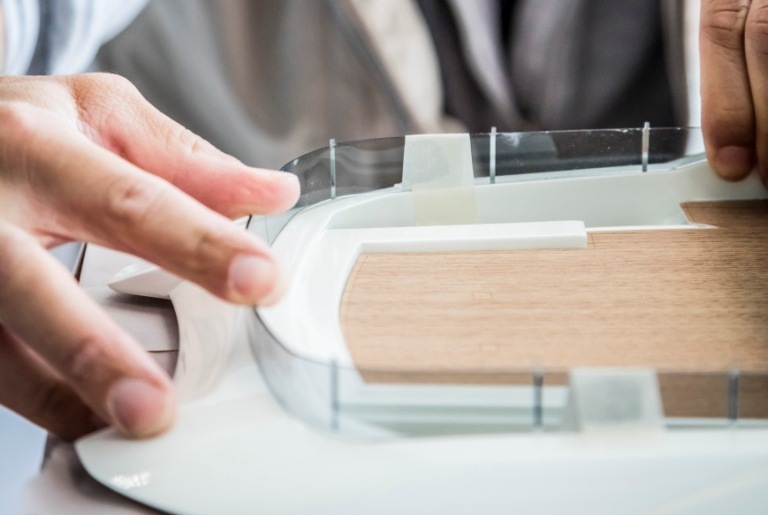
Interview with Mario Moses (Project Development Specialist)
As Project Development Specialist, what can you say about the various type of printers, how are the various manufacturing methods chosen?
MM: “The choice is made according to the part to be realised, the complexity of the piece and sizes. When a project can be assimilated to realisations already made, then I decide on the basis of my experience in this role, otherwise for projects with different characteristics we consult with our colleagues and make a common choice: being a team helps us to find different solutions and assess new hypotheses”.
Can you satisfy all your customer’s requests? In which aspects can the customers, so to speak, indulge and in what must they be limited?
MM: “Yes, we have always satisfied our customers so far, even for the most original requests. As regards colour and selection of covering material (teak, glasses, marbles etc.) we have no limits. The main difficulties can be dictated by the minimum seal thickness of each material that we have tested over these years. In addition, the model size and conformation shall be assessed: lights, for instance, need a minimum thickness to be inserted into the model or as spectacular part of the base. But on these aspects, we can always reach a compromise with the customer”.
[divider style=”dashed” top=”20″ bottom=”20″]
The day spent by Model Maker Group was useful to see with our own eyes how the company operates with the same dynamics and with the same professionalism of a real shipyard. Research and development are also here important areas: machineries, working spaces, study of materials along with a team facing every project with attention, involvement and passion, are all essential elements turning a working process into a successful outcome.
Today Model Maker Group is working with the best Italian and foreign boat builders, including lots of the most prestigious names. All the international yacht shows from Cannes, Monaco, Fort Lauderdale to Dusseldorf, Miami, Dubai, Palm Beach and Singapore, are the main appointments where shipyards and architectural firms exhibit the models realised by the company of Itri. A small local reality with an intense activity at global level and a no-stop work cycle, active 12 months a year.